What is asset performance management?
Data capture, integration, visualization, and analytics are all a part of asset performance management (APM), which is designed to improve the reliability and availability of physical assets.
So, what are the primary advantages of keeping track of asset performance based on claim information? In general, you use Content ID to make money by claiming YouTube videos with your content. It’s possible to understand your asset’s revenue and marketability by analyzing it. Claims monitoring has several key advantages:
- Measure your assets’ global impact and monetary return on investment (ROI)
- To compare your claimed assets to those of your competitors.
- Compare the revenue potential of two separate channels you oversee.
- To find out who else is trying to take possession of your assets.
However, Monitoring asset performance from claims has additional advantages. Check it out –
- Asset performance management is an effective strategy to reduce unplanned downtime, maintenance costs, and EH&S hazards. More than just deploying sensors and point software solutions to keep tabs on your systems and assets are required to implement an effective APM approach.
- To get the most out of APM software, firms must have an integrated, linked enterprise solution that can bring disparate data together to identify new trends and insights that enable safer, more dependable operations while supporting optimal performance at lower sustainable costs.
- Organizations that place a high value on their assets might benefit from APM’s data management, pattern identification, forecasting analytics, artificial intelligence (AI), and machine learning (ML). Take data intelligence and visibility to stay one step ahead of disaster.
- Reactive maintenance techniques and condition-based maintenance are still being addressed in many plants and facilities today by using a variety of distinct software solutions that have been amassed over a long period. This circumstance presents a problem because of the lack of integration between such a wide range of instruments, making it difficult to discover new insights.
- A primary strategy to managing production assets that do not consider asset cost, availability, and risk management are likely to lead to underutilization of your assets. Unplanned downtime can cost up to 10 times the amount of money spent on planned maintenance because of lost productivity and interruption of operations. There are TCO (Total Ownership Cost) consequences to consider!
How Do You Keep an Eye on Your Asset Management System’s Performance?
An assessment and monitoring system for the plant’s capital assets is required in all reliability-centered continuous improvement projects.
• Continuous Monitoring
Nonconformities in the asset management system are identified in a reactive monitoring process, and any degradation, failures, or events involving the assets themselves. Sounds simple, but how do you keep track of and measure nonconformities in your management system and physical assets without spending a lot of money.
Physical assets in a business are tracked over their full life cycle as part of an integrated AMS strategy (procurement, commissioning, operations, maintenance, and disposal). A system of processes and procedures governs the long-term planning, production scheduling, and management and maintenance of these assets. As the AMS expands to include all of the company’s assets, how do you ensure that standards are being met?
• Preventative Measures
Physical assets and information systems (AMS) are monitored to ensure that the organization’s needs will be met in the future. The only difference between this requirement and reactive monitoring is the time of day when it comes down to it. Root Cause Analysis and Root Cause Failure Analysis are comparable in this respect. However, the timing of the analysis differs for these two analytical methods that address actual or anticipated issues. Performing it in response to a failure or incident is considered reactive; performing it to prevent one from occurring is considered proactive.
• Indicators that show progress and those that show deterioration
By definition, an AMS that uses lagging indicators is reactive. The AMS must also incorporate leading indicators that predict future non-conformance or inadequacies to be proactive and effective. Too many firms confine their AMS indicators to maintenance or failure-centric weaknesses, focusing on things like preventative maintenance compliance, wrench time, and the effectiveness of maintenance planning. The AMS can only be effective if all parts of asset management are taken into account and tracked, including maintenance, failure, and breakdown performance.
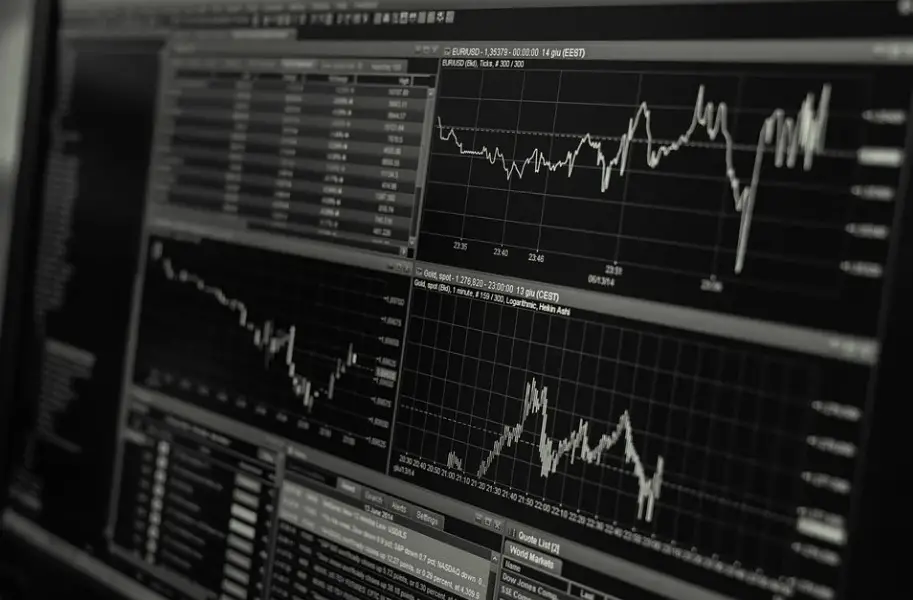