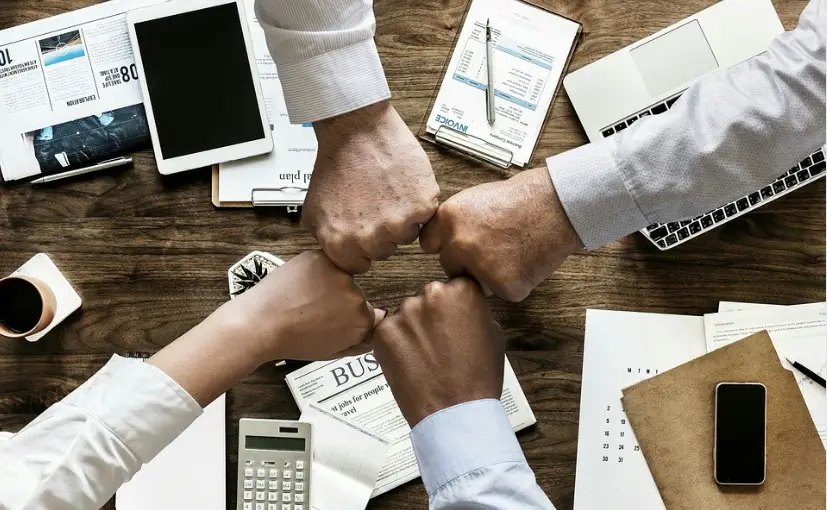
Supply chain management decision areas
Both strategic and operational considerations go into each of the four main supply chain management decision areas that make up the supply chain management process:
- Location,
- Production,
- Inventory, and
- Transportation /distribution.
Let’s check details for a better understanding of supply chain management decision areas.
- The Role of Location in Decision Making
The first step in developing a supply chain is determining the optimal locations for manufacturing plants, distribution centers, and points of origin. Choosing where to put your facilities requires you to make a long-term investment. The possible routes the product takes to the end consumer are fixed once its size, number, and location have been established. Let’s check supply chain management in the dairy industry.
Besides, these choices have far-reaching effects on an income statement, expenses, and quality of service because they depict the fundamental strategy for entering consumer groups. An optimization procedure considering production costs, taxes, duties and duty drawbacks, tariffs, media content, distribution costs, production constraints, etc., should be used to make these choices.
- Making Choices in Production
The assignment of suppliers to production facilities, production facilities to distribution centers, and distribution centers to consumer markets are all examples of strategic choices. As before, these choices have a significant bearing on the company’s profits, expenditures, and quality of service provided to customers. Explore- the importance of supply chain management.
However, these choices are made with the knowledge that the facilities already exist, but they nonetheless dictate the precise routes a product takes to get there and back. The capacity of the manufacturing facilities is another important factor, which largely depends on the level of vertical integration within the business.
Furthermore, Production schedules are the primary focus of operational decisions. Construction of master production plans, scheduling of machine production, and equipment maintenance are all examples of decisions in this category. The volume of work distribution and procedures for quality assurance are two more factors to consider in a manufacturing environment.
However, you can get some tips – on how to achieve strategic fit in supply chain management.
- Making Choices About Inventory
It’s a term for describing techniques used to keep track of stock. Raw materials, work-in-progress, and finished commodities all constitute inventory levels. Also, they may be in transit between two different places. Their principal use is as a safety valve for the supply chain, absorbing shocks and preventing disruptions. Gather more on – evaluation of supply chain management.
However, Effective management of inventories is crucial in supply chain activities since the cost of retaining them can range from 30 percent to 40 percent of their worth. Goals are established at the highest levels of management, making this a strategic endeavor.
Hence, most studies on managing inventory have followed a purely quantitative tack. Push versus pull deployment tactics, control rules, and the establishment of optimal order amounts, reorder points, and safety stock levels at each stocking station all fall under this category. Thus, these factors are crucial because they primarily influence the service consumers offer. Learn more about – the objectives of supply chain management.
- Options for Getting Around Town
The much more significant of these options entails the choice of a mode of transportation. These are heavily linked to stock decisions, as the optimal mode of transport is frequently determined by balancing straight transportation costs against indirect stock costs.
Besides, Air shipments may be the most convenient and cost-effective means of transport because of their speed, dependability, and reduced need for safety stock. While transport by sea or rail can save you money, you’ll need to keep plenty of inventory on hand to account for the unpredictability that comes with it.
Therefore, factors including quality of customer service and accessibility to the decision maker are crucial. Running efficiently is financially prudent because transportation accounts for over 30% of transportation costs.
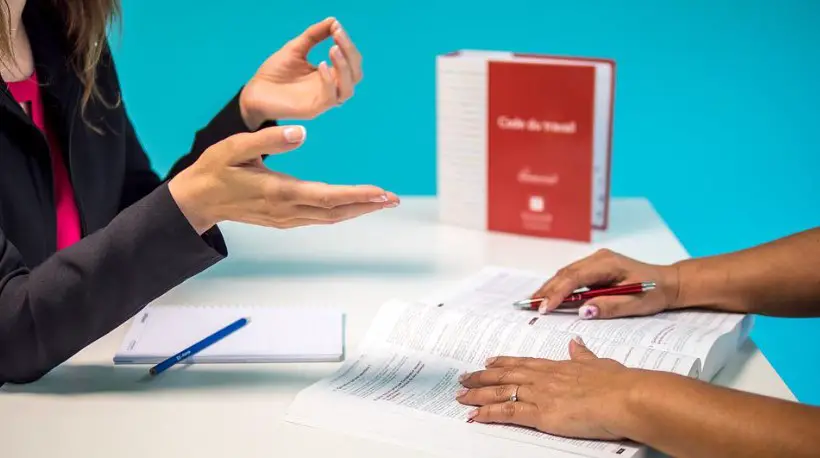